Product Introduction
Suitable for solar panel production line in solar panel factories
The main function of the equipment is to separate the battery string from the glass, lift the battery string with the crane to a certain height, and then suspend the welding of the head, middle and tail of the bus bar of the in-line version module;
It has the function of rolling bus bar for belt and bending U and L leads upward.
Key Attributes
Product Model | CT-HLH-200 |
Beats | ≤18S |
Activation rate | 99% or higher |
Overall yield | ≥99%(according to the component unit, the componentlayout accuracy of the inflow bushing belt weldingmachine should be within ±0.5mm) |
Fragmentation rate | < 0.02%(in pieces) |
Maximum compatible component size | 1650*900-2500*1500mm |
Compatible battery size(mm) | Compatible 156-210mm |
Compatible with number of grid wire roots | Compatible with 5-15 grids |
Power supply | Three-phase five-wire 380V/220V 50/60Hz |
Power | Peak 40KW Average about 20KW |
Air Supply | Pressure 0.6-0.8MPa flow 2000L/min |
Machine size | 5220mmX2570mmX2450mm |
Alarm device | Tri-color light + buzzer |
Deviation correction | 9 camera visual positioning |
Positioning mechanism | Electric cylinder/servo module |
Number of anchor points | ≥5 points |
Positioning method | Mechanical positioning |
Feeding method | Roll loading, automatic cutting, bending |
Roll size | Axle hole 20-25mm, outer diameter < 210mm |
Roll load bearing | ≤13KG |
Compatible bus tape width | Factory supporting 4mm, 6mm |
Compatible with bus tape thickness | 0.18 mm to 0.4 mm |
Cutting accuracy | 0.5 mm or less |
How the lead is made | Bend straight up |
Lead Angle and deviation | 90。 Deviation of 2 to 3。 |
Handling method | Servo motor + vacuum adsorption |
Positioning mode | Mechanical positioning + vacuum adsorption |
Positioning accuracy | Less than 0.5mm |
Distance from bus bar to battery | 2-10mm adjustable |
Busbar overweld strip length | ≤2mm (length error) |
Head life | ≥1 year |
Welding head replacement time | ≤60min |
Mode of operation | Servo motor |
Cooling method | Air cooling |
Welding method | Electromagnetic induction welding |
Number of welding heads | 18 |
Welding head control method | Current control/time control |
Welding heating time | ≤2s |
Welding temperature control accuracy | ± 5 ℃ |
Welding tension | Weld band welding force ≥5N/mm (bus bar and weld band) |
Weld appearance | Molten tin full |
Welding contact area | 80% or higher |
Scar size | ≥(4*4)mm2 |
Control systems | PC+PLC (Reserve 5% of I/O points) |
Communication interface | Meet MES interconnection requirements |
Packaging and delivery
To better ensure the safety of your goods, professional, environmentally friendly, convenient and efficient packaging services will be provided.
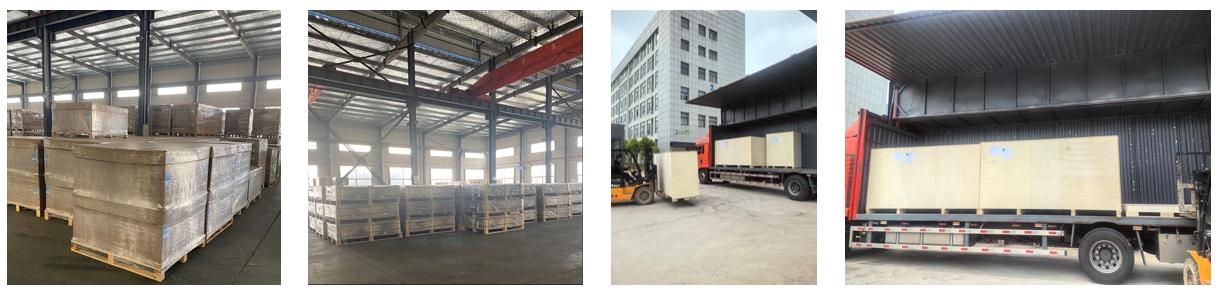